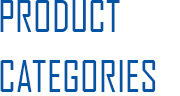
- DHP419 Series of PP Yarn Stretching Machine
- DH419D Series PP FDY Multifilament Spinning Machine HT
- DHP418 Series PP FDY Multifilament Spinning Machine MT
- DHKV 1235-12 Polyester POY Spinning Line
- DHPE Ultra High Molecular Weight Polyethylene Yarn Spinning Equipment
- DHTA Aramid 1414 Yarn Spinning Line
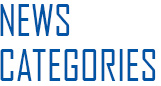
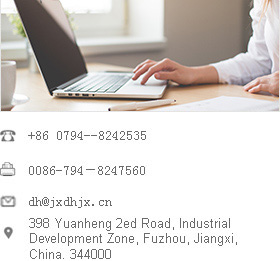
The spinning machine makes the fiber-forming polymer solution or melt form filaments. It adopts the friction transmission method to automatically switch the cake through the automatic switching mechanism. The lifting cylinder supports the friction roller device and the groove roller device for vertical lifting. movement. All electrical devices are centrally controlled by a programmable controller, which effectively guarantees the stable tension of the cake during molding, good molding, and high production efficiency. It is a key equipment in the production process of spandex spinning.
The spinning machine is between the original yarn guide and a drafting machine. The tow passes through the oil immersion tank under low tension. The oil in the tank is heated to 40-50°C in order to make the tow uniformly obtain the continuous drafting needs. To ensure the smoothness and cohesion of the tow and keep the temperature of the tow constant.
The three pieces of yarn of the spinning machine enter a drafting machine, and the drafting roller of the drafting machine serves as a guide and fixes the position of the tow during the drawing process. After leaving a drafting machine, the tow enters the water chute and immediately enters the behind wet drafting state. The tow is in the second drafting zone, that is, between the second drafting machine and the tension heat setting machine. The stereotype treatment is obtained at high temperature, and the complete orientation of the macromolecular structure is obtained. The two-pass drafting completes the draft ratio of about 15% to 20%. This process can obtain high strength and low elongation, low shrinkage and high modulus characteristics.
The tension heat setting machine of the spinning machine consists of 18 large cylinders, followed by three drafting machines. The tension heat setting machine is divided into three zones that can be started independently. This can adjust the shrinkage and slack levels appropriately between these four-roll heat-setting areas. If producing wool-type low-modulus products, there is no need for intense heat setting, and the tow can pass through these large circles without heating. cylinder. The cooling work is completed by the tow cooler. The oil sprayed on the tow takes the maximum amount of heat away from the fiber due to steam. The tow then enters the cutter under uniform tension and is cut to the required length. The cut fiber is sent to the baler to make the finished bun.
Jiangxi Donghua Machinery Co., Ltd. focuses on the production of polypropylene spinning machines, polypropylene medium-strength spinning equipment, polypropylene high-strength spinning equipment, polypropylene FDY spinning machines, polyester spinning machines, aramid 1414 fiber spinning equipment, DHP419 series high-strength polypropylene Spinning drafting machine, polypropylene spinning machine, DHP418 series polypropylene spinning drawing machine, DHkv1235-12 type polyester spinning machine, DHPE type high strength high modulus polyethylene fiber spinning equipment, DHTA type aramid 1414 fiber spinning equipment, HDZF3 High-vacuum dynamic drying-solid-phase thickening integrated machine, polypropylene spinning machine.